Fuel gases have been used in manufacturing for decades and is a very common part of the process. Are we well-informed enough to make the best choice of fuel gas for oxyfuel cutting?
When supplying used and refurbished profile cutting machines we are often asked about gases and we recommend you call in your Gas Supplier and discuss the options as getting it right will cut down your costs of production.
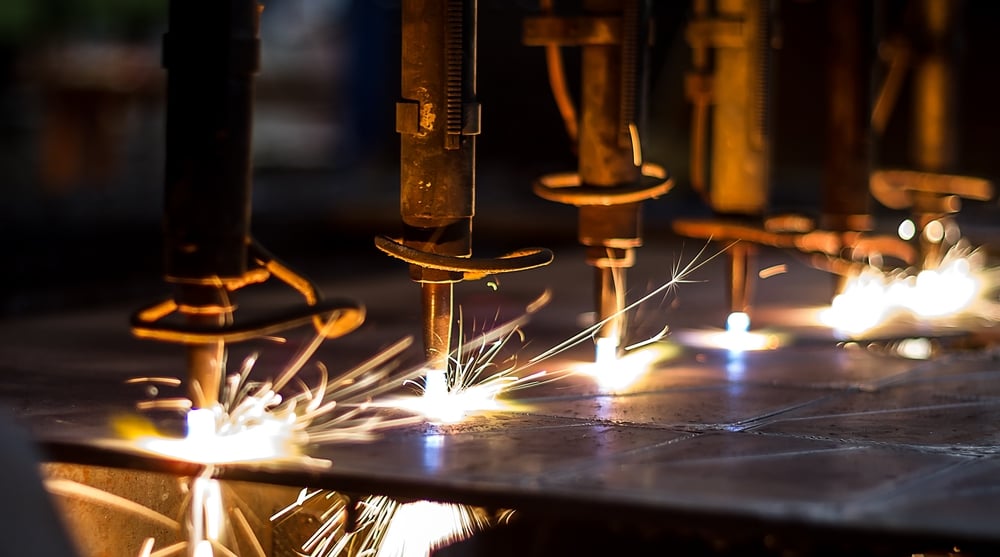
Do fabricators know about what has become such a common part of the manufacturing process?
I found this article on thefabricator.com and thought I would share with our readers.
Oxyfuel cutting is a process used to sever steel via a chemical reaction of oxygen with the base metal at elevated temperature. Once oxygen is mixed with a fuel gas, the temperature rapidly increases to a point high enough to melt and wash away the steel. The oxyfuel cutting process is nothing more than rapid oxidation—also known as burning.
Of course, cost is always a concern for fabricators, and the cost of fuel gas—whether acetylene, propylene, or propane—typically represents 20 to 25 percent of the total cutting cost.
The following comparison of the three fuel gases applies to their use in cutting carbon steel, which melts at around 2,760 degrees F. To compare the gases accurately, fabricators must take into account their heat transfer properties, flame temperature, oxygen consumption, heat distribution, safe operating pressure, shipping, and handling. And fabricators must ensure they have the proper tip size and style, gas hose, and regulator setting for the application.
Acetylene
Acetylene, first discovered in 1836 by chemistry professor Edmund Davy, has been used for cutting for more than 100 years. When combined with the proper amount of oxygen (1-to-1), it has the highest flame temperature—in excess of 5,800 degrees F with a neutral flame temperature of 5,580 degrees —and the lowest secondary flame temperature. The job of the secondary flame—the larger outer bulb (usually blue) surrounding the inner white flame column—is to preheat the steel for the melting or cutting action of the inner (primary) flame.
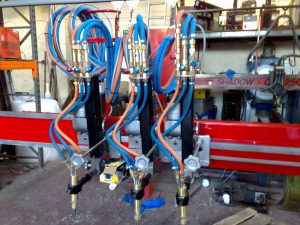
The heat content of acetylene, at 1,470 BTU per cubic foot, is the lowest of all fuel gases except natural gas. With a low secondary flame temperature, the gas can require significant preheat time in heavy cutting applications.
What makes acetylene so different from the other fuel gases? For one thing, the gas cylinder is not an open cylinder. Acetylene is an unstable, shock-sensitive gas. A cylinder filled with raw acetylene would blow itself apart if it weren’t stabilized. Internally the cylinder is filled with an absorbent during the manufacture of the cylinder. Typically, this absorbent in newer cylinders is calcium silicate, similar to sand.
Before the acetylene filling operation, the cylinder is filled to about 80 percent with acetone, the stabilizing agent. Next the cylinder is connected to a manifold system, and the acetylene gas is produced when calcium carbide is exposed to water and slowly injected into the cylinder to be absorbed by the acetone. The acetone holds the gas in solution—a liquid absorbing a gas.
Acetone is extremely flammable, so acetylene should never be used in excess of 15 pounds. If the acetylene withdrawal rate is more than 15 lbs., the acetone can’t release the gas fast enough, so the process sucks acetone out in addition to acetylene. That’s a big safety concern; acetone will slowly dissolve the fuel gas hose from the inside out, plus liquid fire will drop from the torch. For this reason, never lay the cylinder down for use. It must stand upright for about two hours before use to ensure the contents are stabilized.
The safe drawoff from an acetylene cylinder is no more than 1/7 of the cylinder volume; some experts have decreased that to 1/10. A higher withdrawal rate will upset the balance of acetone in the cylinder and increase the possibility of drawing off acetone through the regulator and fuel gas hose.
When these rules aren’t followed, acetylene is the second most dangerous gas in industry after oxygen. It has a tendency to backfire. If the flame is grounded out on the base metal, it will appear to go out, but it actually is burning back inside the torch—an occurrence known as flashback. New torches generally have built-in flashback arresters to prevent burning from going backwards into the hose, but a flashback burns very fast and is a very serious condition.
Like all fuel gases, acetylene’s cylinder content pressure depends on the ambient temperature. A full cylinder at 0 degrees F has a gauge pressure of about 85 PSI; at 60 degrees F, gauge pressure averages 225 lbs.; at 100 degrees F, gauge pressure is 355 lbs. Pressure above 300 lbs. is not acceptable, so cylinders should not be stored in direct sunlight.
Regardless of these concerns, acetylene has several good qualities that the other fuel gases don’t have. Even with its very economical oxygen consumption (1-to-1), it delivers a hotter neutral flame than propylene and propane. Acetylene is the only fuel gas that can be used for gas welding. It is great for flame spraying, hardfacing, preheating, and soft soldering of copper. Acetylene works better in mini- and microtorches than the other two gases, and it can be used in a single-hose air aspirator torch. Contact your gas supplier for the required fuel gas hose grade.
Propylene
Propylene has rapidly become the most preferred oxyfuel gas in the industry. Found in nature as a byproduct of oil refining and natural gas processing, propylene has been used in the metalworking industry since the early 1970s.
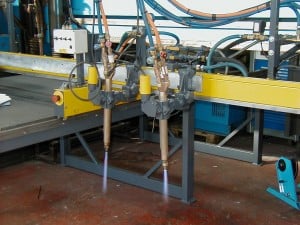
The torch tips and fuel gas regulator for propylene are different than for acetylene. The nut and nipple are both CGA-510 (a Compressed Gas Association connection fitting standard), but the delivery gauge is not redlined at 15 PSI. The two regulators also are ported differently. Propylene and propane can be used at cylinder pressures, but the delivery gauge should be set at the required pressure for the intended use. More is not better; it affects cut quality.
Propylene has a high heat release in the primary and secondary flame. The secondary flame has more than twice the BTU content as acetylene, at 1,960 BTU/ft.3 The primary flame has 440 BTU/ft.3—similar to acetylene. Total flame BTU content is about 2,400, twice that of acetylene.
Compared to acetylene, propylene will last five times longer. Propylene, at any temperature, has the highest vapor pressure and withdrawal rate of any of the liquid fuel gases. A neutral oxyfuel flame temperature is about 5,280 degrees F, about 300 degrees F cooler than acetylene.
As with acetylene, propylene and propane require cylinders manifolded together for big jobs that need large heating heads with a high volume of fuel gas. The liquid fuel in the cylinder cannot boil off fast enough if the withdrawal rate is more than 90 ft.3/hour.
Propylene is a very stable gas, with a slight tendency to backfire. Oxygen usage for a neutral flame is 3-to-1. With its higher-temperature secondary flame, propylene cuts faster than acetylene, and it typically produces less slag.
A 100-lb. cylinder of propylene is about 23.4 gallons, or 922 ft.3 of gas at 70 degrees F.
Propane
First identified in 1910 by the U.S. Bureau of Mines, propane is a byproduct of natural gas processing and petroleum refining. It is more widely used than the other two industrial fuel gases in such applications as automotive fuel, home heat, cooking stoves, gas grills, and grain drying.
The U.S. standard for commercial propane is 90 percent propane and 10 percent fillers (ethane, butane, ethyl mercaptan, and propylene). One of its most desirable traits is that the product of the burning process is water vapor and carbon dioxide.
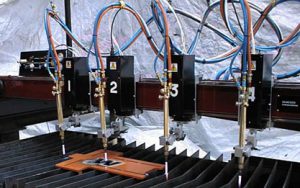
Propane expands 1.5 percent per 10-degree-F rise in ambient temperature. In other words, propane will expand 15 percent from 0 to 100 degrees F. Therefore, a propane cylinder cannot be filled to more than 80 percent of its internal space; it requires a head space over the liquid propane in the cylinder for temperature expansion. The liquid propane also needs room for when the propane vapors are drawn off for the gas consumed by the torch burning. The liquid gas in the cylinder will boil into a gas vapor needed to produce a flame. It is a continuous action as the vapor pressure is consumed. As with propylene, the torch burns a vapor gas, not liquid.
If the heating tip consumes more than 85 ft.3/hour of gas, two cylinders will need to be manifolded together. Not enough gas can boil off to meet the supply required for the torch burn rate. Starving the torch will cause it to overheat.
Heating torches that use a single hose from the regulator to the torch are commonly used with propane. These torches can produce 1 million BTUs. No oxygen is needed. This is a very economical way to preheat heavy plate and castings 900 degrees F or more in a very short period of time.
Propane is sold by the pound in commercial cylinders. It has a 4-to-1 oxygen-to-fuel consumption for a neutral flame. Propane’s single flame temperature is 1,750 degrees F, and its oxyfuel flame temperature is 4,820 degrees F.
This gas has only a slight tendency to backfire. Its primary flame contains 255 BTU/ft.3; the secondary flame is 2,240 BTU. Like propylene, propane requires a two-piece cutting tip; the torch heating tips are not the same as for acetylene and cannot be interchanged.
Many variables need to be considered to compare the common fuel gases on a technical level. But the fundamental information presented here at least should give any fabricator a start when considering a purchase of a flame profile cutting system. But don’t forget to get advice from your Gas Supplier
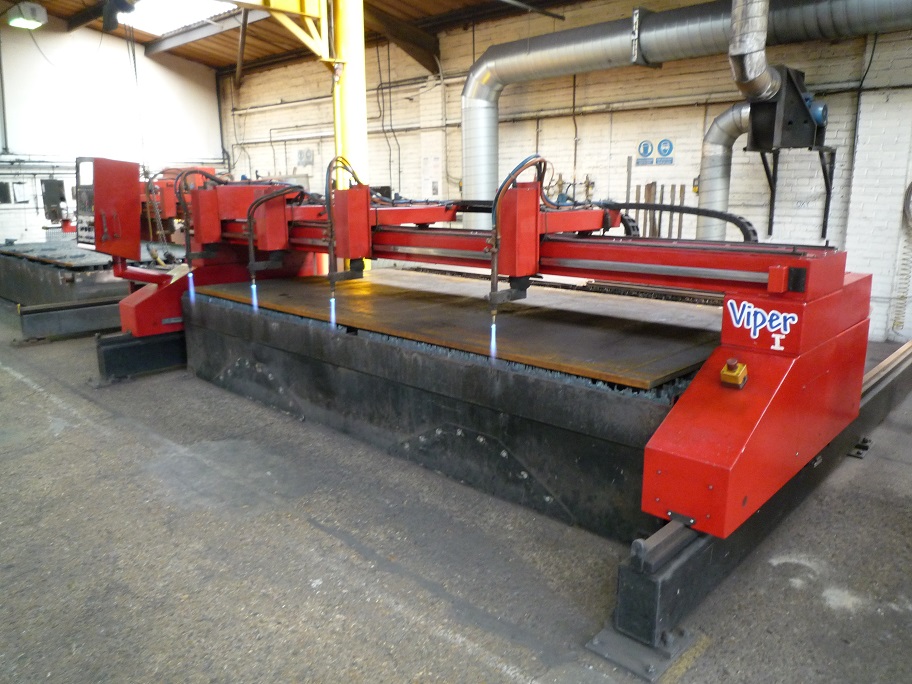
If you’re considering purchasing an OxyFuel CNC cutting machine take time to view the affordable, robust used and refurbished profile cutters for sale on our web site and a link to a video showing the refurbishment work that takes place.
We only sell machines that were made to last. If your budget allows we refurbished to order and you will be presented with an excellent heavy duty profile cutter – a fraction of the cost of a new – like for like – machine.
We buy and sell machines ranging from 8’x4′ cutting capacity with a single torch to 5m track length systems with either or both Gas and Plasma cutting torches fitted.
Our CNC cutting machines are bespoke, include warranty and can be delivered anywhere in the world. All made by the leaders in the field ESAB, Esprit, SAF, BOC, Victor, Koike and Messer MG, Burny and Hypertherm you will be pleasantly surprised at the price and delighted with the quality.