Welding is among the most influential industrial processes affecting renewable energy production. If you use less-than-adequate equipment, project delays and added costs are far more likely. Likewise, correctly selecting a welding process is critical for high productivity and minimising rework.
Solar, wind, hydropower, hydrogen, and ammonia green energy generation are very different, and so are the used welding processes, equipment, and production challenges.
Key Takeaways:
- There’s a rapid growth Worldwide in consumption of energy from renewable sources
- Welding plays a key role in all forms of renewable energy production
- Wind farm manufacturing requires heavy-duty, welding automation equipment capable of welding thick, heavy-walled steel.
- Solar welding projects depend upon precision and prevention of distortion, to ensure structures are as straight as possible.
- Welding in hydro projects is very complex, and is required in regular maintenance of hydro plants, as well as initial production phases. Long service life is key for these critical parts.
- Innovative new clean energy sources like green hydrogen rely on appropriate storage tanks and vessels, needing the highest quality welds to produce them.
Contents:
- Introduction
- Welding for Wind Farm Projects: How a Wind Turbine is Made
- Welding Equipment for Wind Towers
- Welding for Solar Projects
- Welding Equipment Used for Solar Structures
- Welding for Hydropower Projects
- Welding Equipment Used for Dam Structures
- Repairing Turbine Blades & Other Worn Parts in Hydro Dams
- Welding for the Green Hydrogen & Ammonia Industry
- Conclusion
Introduction
The share of primary energy consumption from renewable sources is quickly increasing worldwide. In 2023, the European Union as a whole led with 21.98%, closely followed by the United Kingdom with 20.52%, while the world in total was at 14.56%, China with 16.16%, and the USA with 11.66%. However, what all of the major countries (and even many smaller countries) share is a rapid growth in renewable energy consumption. Just take a look at the graph below!
With a near-vertical parabolic growth in renewables, there’s a whole lot of welding to be done globally. Structural supports for solar, wind towers, piping and turbine systems for dams, pressure vessels, and many other components must be welded on and off-site.
Welding For Wind Farm Projects: How Is A Wind Turbine Made
On and offshore wind farms require extensive welding to fabricate their wind towers and foundations. However, since wind towers are made from very thick steel (often above 80 mm thick), any weld defects can be very costly to repair.
Wind towers and foundations are made from rolled steel plates. First, the plates are rolled into cylindrical cans that are seam-welded. Next, individual cans are aligned and joined to each other with circumferential welding, forming the tower body or foundation.
Foundations are the most critical and complex parts of the wind towers. They can be as simple as monopiles or as complex as jacket and tripod structures for offshore wind farms deep in the ocean.
Welding Equipment For Wind towers
Wind farms require heavy-duty welding automation equipment that can handle thick, heavy-walled steel. Most of the welding is done using submerged arc welders (sub-arc or SAW). The SAW process can deliver the extreme weld metal deposition rate and heat necessary for the wind farm thicknesses.
However, many wind power components, especially TKY joints of the foundation structures for offshore wind farms, require MIG and Flux-cored welding too. So, a multi-process, SAW/FCAW/MIG power source can provide all the welding methods you may need. For example, the Lincoln Idealarc DC 1000 Power Supply that we sell or rent for your convenience.
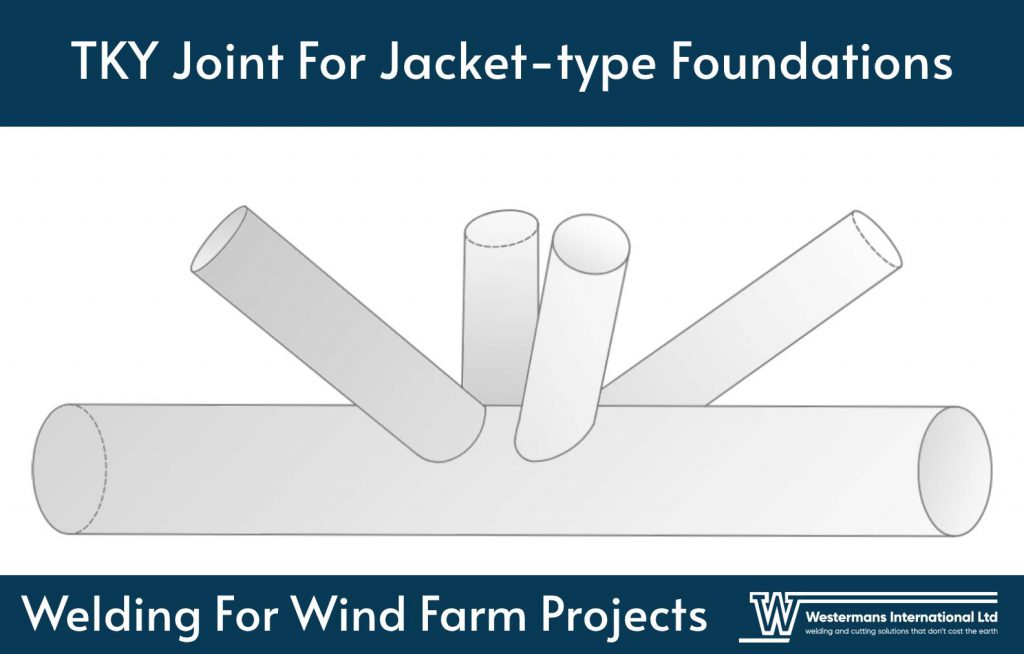
The welding power source is only a part of the setup. Wind turbine towers require highly accurate longitudinal and circumferential welds on thick steel. So, you need precise equipment to automate these welds for standardised repetition. This is where the column and boom welders and welding rotators come in.
Rotators use wheels to align the two cans, while the column and boom carry a SAW welding head to the joint. The SAW head is stationary as the rotator rotates the two cans, ensuring a circumferential weld. Or it moves longitudinally to produce a seam weld.
You must also accurately preheat and conduct post-welding heat treatment for tower fabrication, especially for critical parts like TKY joints and other sensitive spots where internal stresses can concentrate. That’s where induction heating systems come in, as they can align with the joint’s shape and heat the material from within, ensuring a highly uniform thermal gradient.
Welding For Solar Projects
Solar panel arrays on fields or rooftops are supported by mounting structures made from non-corrosive materials. These structures must be welded with high precision and minimal heat input to prevent excessive distortion.
You don’t want difficulties aligning the solar panels with the supports, brackets, and custom elements. Since solar panels and their frames are rigid, the support structure must be as straight as possible. Likewise, weld defects can lead to weld failure due to weight from the panels and snow and the impact of the wind. To prevent buckling and structure failure, welds holding the structure must pass all quality inspections.
Welding Equipment Used For Solar Structures
Solar panel supports are welded on-site and in the fabrication shops. Considering the relatively low thicknesses of the frames, beams, brackets, and other supports, the MIG and Flux-cored welding processes will provide the best ratio of productivity and weld quality. For field work, you can opt for self-shielded flux-cored wires or the stick welding process. However, you’ll need to use MIG or TIG welding for aluminium mounting structures and customised parts.
Multiprocess welders can provide all the processes you need for galvanised steel, stainless steel, or aluminium, depending on the parts you work with and their material. However, solar farms are often placed in remote areas. So, using diesel welders will give you the electrical power for welding even if there’s no power available.
Welding For Hydropower Projects
Hydropower projects are vastly more complex than wind and solar and can require using almost all welding processes. Dams use advanced turbines of various types and sizes to convert the kinetic energy of water. Likewise, hydropower relies on massive shafts, disks, runners, guide vanes, casings, piping, penstocks, massive trash racks, intakes, spillways, and customised structural components. There is A LOT of welding for many critical elements of a hydroelectric dam.
Besides initial production, welding in the hydropower industry is highly employed in regular maintenance.
Did you know hydro turbines can shed about 1 kilogram of metal daily due to immense water pressure and cavitation? Yes, that much. So, turbines and other components must constantly be repaired and maintained with welding, including surfacing and other applications.
Cavitation occurs when a bubble collapses on itself, producing a high-velocity microjet that hits the surface of the turbine, causing a microfracture. With time, these jets will absolutely obliterate the turbine through pitting erosion. Watch the video below from the Institute of Energy Technology to see how powerful it really is!
Cavitation is just one example of a damage mechanism in hydro dams. There are plenty more. So, welding is irreplaceable for maintenance and keeping the plant running optimally and safely. You could safely say that if you stopped weld repairs, a hydro dam would quickly be done for.
Welding Equipment Used For Dam Structures
Welding various dam components requires using MIG, FCAW, TIG, MMA, and SAW, welding power sources. Likewise, you’ll need to use multiple welding automation equipment, depending on what part of the hydropower equipment you are fabricating or repairing.
When welding massive steel penstock vessels that can be several kilometres long and over 2.5 meters in diameter, the welding process must be highly precise. These high-pressure pipelines guide water into the turbine and must have extreme resilience and support a long service life. Depending on factors like the penstock thickness and material, you can use the MIG, FCAW, MMA, and SAW for welding individual pipes into a penstock pipeline.
Penstocks are often partially fabricated in a workshop, primarily using the sub-arc welding equipment for their high productivity and weld deposition. Next, penstock pieces are delivered on-site and welded together using powerful stick welders or automated MIG/FCAW or TIG equipment. Automated carriages and orbital welding solutions can drastically improve welding productivity and reduce weld defects.
Here’s a video of penstock welding in Kenya using Gullco KAT automatic welding oscillators we supplied to Heavy Engineering:
Repairing Turbine Blades And Other Worn Parts In Hydro Dams
Cavitation and metal erosion in hydro dams is a very complex issue because multiple wear mechanisms can work together or individually. So, your response must tick all boxes specific to the plant and its environment.
While complex, an appropriate hard surfacing alloy selection and an adequate weld cladding method application will return the hydropower plant to its original efficiency.
Weld cladding machines, laser cladding, and manual welding applications are used to deposit highly specialised hardfacing alloys to rebuild worn metal surfaces.
Welding For The Green Hydrogen And Ammonia Industry
Both green hydrogen and green ammonia can be clean energy sources if the electricity used to split water and hydrogen is sourced from renewable sources like wind, solar, or hydro.
Green ammonia/hydrogen is like a “battery” that can store energy from renewable sources. However, green ammonia has a higher potential for use than pure hydrogen, as it can be stored more easily. Green ammonia first requires producing green hydrogen. Next, this hydrogen is combined with atmospheric nitrogen, producing green ammonia in Haber-Bosh synthesis.
For green hydrogen and ammonia production, you need storage tanks, pressure vessels, pipelines, and other processing and storing equipment. Likewise, transporting green ammonia requires specialised storage tankers. So, welding plays a significant role in the cost-effectiveness and reliability of production and storage.
Cryogenic storage tanks and pressure vessels require exceptional weld quality to ensure safety, especially when hydrogen is involved at extremely low temperatures. Therefore, weld quality must be nearly perfect, requiring advanced welding automation.
Automated welding tractors, orbital welders, and welding manipulators in combination with the rolling systems, are critical for producing the vessels and storage required for the green hydrogen and ammonia. These projects can be costly. Any weld defects can delay the project and amplify costs. Automation can help avoid unnecessary waste and ensure maximum weld accuracy and quality. Since these tanks and vessels must be made from exotic alloys, automation becomes even more critical.
Conclusion
Green energy is a complex field, especially when you peek behind the curtain in the fabrication sense. A vast number of parts must be produced and maintained, and each benefits from choosing the most appropriate welding method and equipment. We are here for your fabrication equipment needs in the Renewable Energy Sector. With a 30,000 sq. ft facility and a massive fleet of welding and cutting solutions, we can help you use the most effective fabrication technologies for any renewable energy project, having helped many contractors and other stakeholders in the field. Contact us today, and our experts will work with you to choose a suitable solution for your specific needs.