Updated January, 2025
Key Takeaways:
- Seam welding is a technique for joining metal components.
- There are two types of seam welding, resistance seam welding and arc seam welding.
- Seam weld variations include spot welds, butt welds, lap welds and flash welds.
- Applications and industries include automotive, aerospace, construction, ship building, and ventilation.
- The process can be manual or robotic (automated).
- A multitude of factors need to be considered when choosing the right seam welder for your needs.
Contents:
- Introduction – what is seam welding & how does it work?
- Seam welding types
- Seam welding applications
- Benefits of the seam welding process
- Safety precautions for seam welding
- How to choose the right seam welder for you
Introduction: What is Seam Welding and How Does it Work?
Seam welding is a technique used to join two metal surfaces together, and is a popular process for joining metal components due to its speed, reliability, and cost-effectiveness.
There are two main types of seam welding, resistance seam welding and arc seam welding. Resistance seam welding heats both metal surfaces, then applies pressure using top and bottom electrodes – the “resistance” then forms the weld. Arc seam welding uses an electric current provided externally (welding power source), to create an arc between two electrodes that are then placed onto the metal surfaces. The heat of the arc melts the metal surfaces, allowing the joining process to occur. By understanding these seam welding processes, you’ll learn which is right for your application, ensuring your welds are strong and reliable every time.
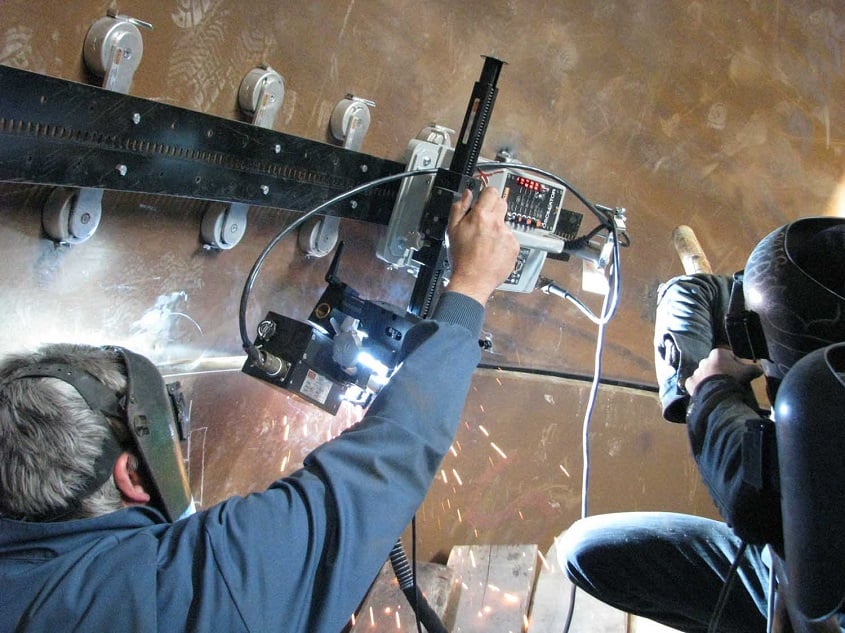
A Closer Look at the Different Seam Welding Types.
Seam welds are used to join the edges of the two pieces of metal, with several types, each has its own advantages and disadvantages. These include spot welds, butt welds, lap welds and flash welds, offering benefits in various applications (see our article on comparing spot and seam welding) and industries.
Spot welds are a resistance welding process, and are used to join two metal sheets by applying heat and pressure at localised points. Spot welding is ideal for welding thin sheet, but isn’t suitable for material thicker than a few mm.
Butt welds are a type of fusion welding, where the joint is fused together at their ends, and in the same plane. Often used in pipe welding and rail welding, where joints need strength. It’s an ideal process for joining long sections of metal. The heat source comes from an arc welding power source (e.g. TIG, MIG etc.)
Similarly, flash welding is also used for this kind of work, but uses an electrical arc produced by the resistance method as opposed to an exterior source (i.e welding supply). It’s a popular process for joining metal rods, rails and pipe in construction.
Lap welding is where the join is created with one sheet overlapping the other, and is beneficial for joining metal sheets of differing thicknesses, but not thicker material. Both resistance and arc seam welding are suitable for producing lap joints, multiple spot welds can be used to hold the join together, or a fillet weld can be produced along the seam. It is common to see both single, and double lap joints when more strength and greater stress distribution is required.
Seam Welding Industries and Applications.
Popular applications for seam welding include:
- Automotive Manufacturing – for producing sheet metal components in car bodies, fuel tanks, and exhaust systems
- Aerospace Industry – seam welding provides leak-proof joints for fuel tanks, as well as panelling
- Oil and Gas – Pipes and pressure vessel joints are often produced using seam welding
- Marine & Shipbuilding – both resistance and arc seam welding processes are used in manufacturing hull compartments, as well as watertight seams for other components.
- Appliance Manufacturing – resistance seam welding is used to produce common appliances like washing machines, refrigerators and air conditioning units.
The Benefits of Seam Welding.
Seam welding can be a manual or robotic welding process. Offering many advantages over traditional welding processes.
Robotic or automated seam welding applications are becoming popular in many industries like automotive, aerospace, and medical device manufacturing. This technology allows for faster production times, higher quality welds, and greater consistency between parts. It also eliminates the need for manual labour, which can be costly and time consuming.
Seam welds are also beneficial for reducing the amount of material waste generated during manufacturing processes, so is also beneficial from an environmental stand point.
Seam welding equipment costs are also relatively inexpensive when considering the time it takes to see a return from the initial outlay. Consumable and maintenance costs are also fairly cheap compared with other processes.
What Safety Precautions Should be Taken When Performing Seam Welding?
Seam welding is an essential process for many metal fabrication shop. But it can be a dangerous process if proper safety precautions are not taken. Therefore, it is important for welders to understand the safety tips to follow when performing seam welding.
Safety precautions for seam welders include:
- wearing protective gear such as gloves, goggles, and face shields
- maintaining proper ventilation in the work area
- ensuring that all tools are in good working condition and properly maintained
- keep flammable materials away from the welding area
- take extra care when working with metals that may contain hazardous chemicals or materials
How to Choose the Best Seam Welder For Your Project?
Choosing the best seam welder for your project can be a daunting task. It is important to consider several factors before making a decision. These factors include the type of welding that needs to be done (whether longitudinal or circumferential seam welds), the size of the project, and the budget available. Additionally, there are various types of welders available on the market and each type has its own advantages and disadvantages. It is important to understand these differences in order to make an informed decision when selecting a welder for your project. If you’d like any advice when deciding on a seam welder machine to meet your needs, contact the team and we will be happy to help!
Did you know we also buy used seam welding machines? Complete our form with machine details and the team will get back to you.
comments
Pingback: A Guide to Understanding Its Applications. – Tracktodirt.com
Pingback: A Guide to Understanding Its Applications. – Mynewcaraccessories.com