The oil and gas industry was responsible for 54.7% of global energy consumption in 2023, and that number isn’t likely to go down quickly. While not renewable, oil and gas play a major role in our lives.
In the UK in 2023, 74.22% of energy use per capita was from fossil fuels. Japan, USA, China, Australia, and India all sit in an 81-89% range of fossil fuel use per capita in 2023. Naturally, such a vital industry requires a lot of maintenance and development, and welding is the most critical technology that can make or break the reliability and sustainability of all systems in the industry.
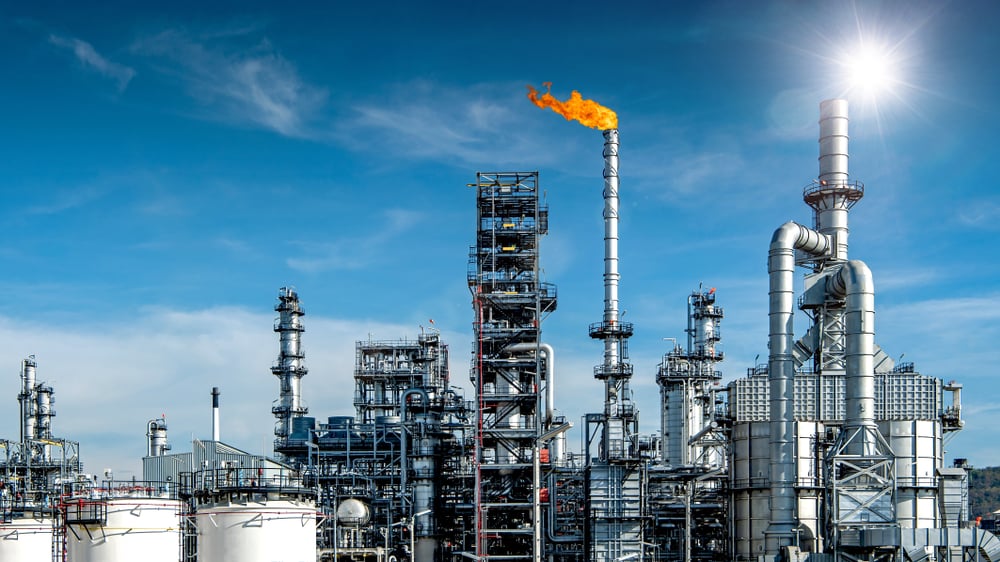
Key Takeaways:
- Welding’s Critical Role:
Welding is foundational for the construction and maintenance of pipelines, rigs, and pressure vessels across the upstream, midstream, and downstream sectors. - Advanced Materials and Techniques:
High-performance alloys like stainless steel and nickel are used alongside advanced welding methods such as TIG, MIG, and submerged arc welding to meet extreme environmental demands. - Automation Enhances Efficiency:
Technologies like orbital welders, pipe rotators, and welding tractors improve safety, precision, and productivity, while reducing costs. - Global Energy Reliance:
Countries like India, China, and the USA heavily depend on oil and gas, underlining the importance of robust welding for infrastructure sustainability. - Quality and Safety Compliance:
Strict industry standards require preheating, post-welding treatments, and precise execution to ensure safety and prevent defects. - Partnering for Success:
Access to modern welding equipment, such as that provided by Westermans International, is key to optimising performance and meeting industry demands.
Without advanced welding processes and automation equipment, oil and gas would cost more. Likewise, refining oil and gas into cleaner versions wouldn’t be possible. Don’t want excessive sulphur originating from the tailpipe of your car? That requires desulphurisation reactors, which operate at high heat and immense pressures. Both of which aren’t doing any good for the welds holding the reactor together. So, you must weld them well, which isn’t easy considering the used alloys. Not just any alloy will endure corrosive and harsh oil/gas compounds at high pressure and heat.
The bulk of the issue comes down to: we want higher efficiency fuel with less pollution. This usually introduces additional extraction or refinement equipment and processes. The better effect we try to achieve, the more complex the process, requiring more sophisticated welding for the process equipment. Therefore, welding often serves as a catalyst for progress in the industry!
Welding Processes Used In The Oil And Gas Industry
Nearly every welding process is used in the oil and gas industry. However, the largest share of welding is done with stick, flux-cored, MIG, TIG, electro-slag, and submerged arc welding. You might see specialised applications using laser, electron beam, friction stir, and similar advanced processes. However, welding in oil and gas is mainly done with advanced arc welding equipment.
Oil And Gas Industry Sectors And Welding Applications
The oil and gas industry is massive. It wouldn’t be possible to name every specialisation and niche part of it in one article. However, oil and gas is principally divided into three sectors: upstream, midstream, and downstream. All three are juggernauts of their own but are entirely dependent on one another.
Upstream: Exploration
Upstream of the oil and gas industry revolves around exploration and extraction of raw crude oil and natural gas. It’s the beginning of the fossil fuel journey. Arguably, the upstream environment is the most challenging, requiring people and equipment to handle rough seas, corrosive environments, and overall demanding conditions.
Oil and gas are extracted using on-shore (land) and off-shore (sea) facilities like rigs and platforms. Offshore drilling is in every way more challenging and costly. But, large offshore wells present a tremendous opportunity for oil and gas producers. Both, land and offshore extraction are critical for oil and gas production.
Welding in the upstream sector is highly diverse. It’s a mixture of welding on-site and fabricated elements delivered for assembly. The most complex welding tasks are the fabrication of massive support structures for offshore rigs and extraction assemblies.
Submerged arc welders are used with welding manipulators to fabricate massive offshore structures like jack-up rigs and jacket-type structures. Another critical welding method for upstream is weld cladding. These systems reduce the costs of riser pipelines and vessels exposed to corrosive agents. Weld cladding lines the inside/outside of the vessel with corrosive-resistant alloys (CRAs) like nickel alloys, reducing the cost of the pipe and vessels and offering high corrosion resistance.
Commonly welded equipment:
- Underwater pipelines and risers
- Oil and gas wellheads
- Subsea tree assemblies (AKA. Christmas trees)
- Blowout preventers
- Offshore platforms and jacket-type structures with various decks, hulls, topside modules, and processing equipment
Commonly welded materials and alloys:
- Stainless steel (austenitic, martensitic, duplex, super duplex)
- Nickel alloys, like nickel-chromium-molybdenum
- Titanium alloys
- Carbon steels
How Do Oil Drilling Rigs Work?
Oil drilling rigs work by drilling into the oil source to create a well for extraction. The drill makes a deep hole in the land or seabed surface. As the hole is drilled, steel pipes are placed inside and cemented in place to create a “casing” inside the line. Once assembled, the oil rigs extract and store the raw product. The pressure inside the reservoir naturally causes the gas and oil to rise to the surface, but pumps and other methods may be used to improve the flow.
How is natural gas extracted? Is the process the same as for oil? While there are differences in equipment and assemblies, the fundamentals of the process are very similar.
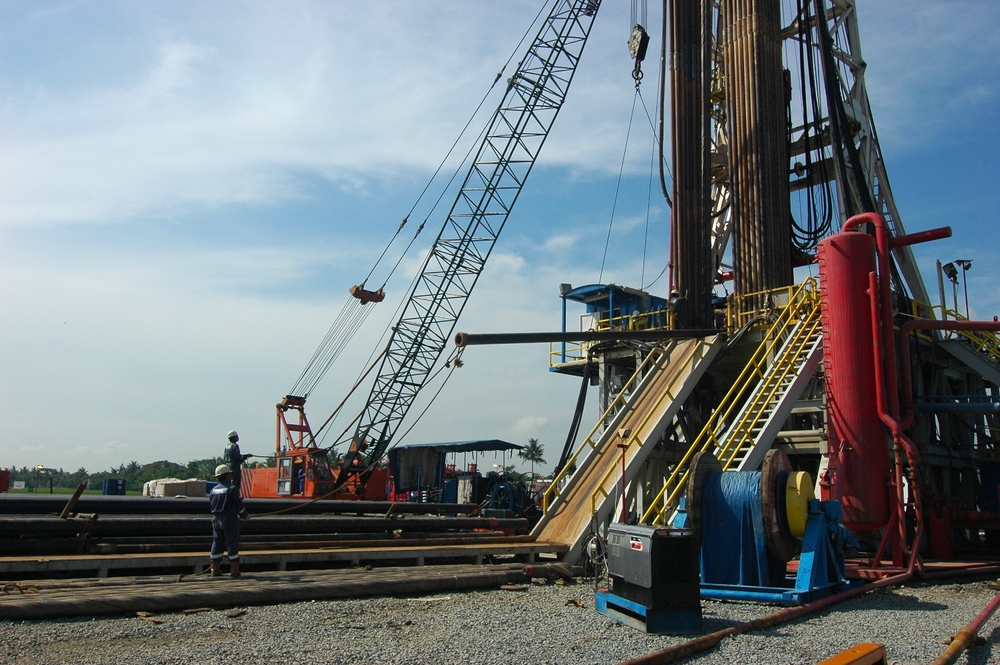
Midstream: Transportation
The midstream of the oil and gas business is mainly about transporting and storing crude oil and gas. The good, old pipelines that span across countries, continents, and even across oceans. These pipes are often massive, thick, and require a whole lot of welding in installation and maintenance.
The United States, for example, has 2.8 million miles of oil and gas pipelines. Pipelines are welded on-site in varying terrain elevations and often in challenging, rural areas. Welding teams must have diesel generators for electrical supply and robust, reliable diesel-powered welders.
Pipeline welding is an industry of its own. While upstream and downstream also require pipeline welding, the term is synonymous with the midstream sector. In fact, the welding professionals who specialise in this sector are often referred to as pipeliners.
Manually, pipelines are welded and repaired using stick, MIG/flux-cored, SAW/ESW, and sometimes TIG welding processes. However, orbital welding systems are irreplaceable for impeccable, repeatable pipe weld quality and significantly higher productivity. Orbital welders, like the Pipeliner 609 Orbital Welder With a Fronius Power Source, are used to weld large, heavy-walled pipe with an open head configuration using MIG/Flux-cored welding. It may not always be worthwhile to purchase such equipment, which is why Westermans International also offers affordable orbital welder rentals.
Commonly welded equipment:
- Transportation pipelines
- Storage tanks
Commonly welded materials and alloys:
- Carbon steel
- Stainless steel (standard austenitic, duplex, and super duplex)
- Nickel alloys, like the 625
Downstream: Refinement
The downstream oil and gas industry refines crude products into ready-to-use energy sources. It’s where the magic happens. Considering the extreme effort and unbelievably complex systems involved in oil and gas refinement, the word magic doesn’t do it justice. Petrochemical facilities are some of the most complex engineering feats humans have ever achieved.
This sector uses the most diverse equipment and alloys. Everything from pipes and tubes of all thicknesses and sizes to complex heat exchangers and pressure vessels—all made from various alloys, including titanium, specialised CrMo steels, and sophisticated stainless steels. Likewise, the aggressors in the petrochemical processes are highly complex and challenging to manage. For example, hydrogen-induced cracking, wet sulfide damage, carburisation, and various types of corrosion attacks are just some factors you must consider when choosing the welding alloy and the process in this oil and gas sector.
Preheating and post-welding heat treatment are usually required for pipe and pressure vessel welding to reduce the occurrence of hydrogen cracking and relieve residual stresses. Strict codes and best practices mandate accurate heating with a uniform heat gradient. Traditional open-flame heating poses a safety hazard and can hardly achieve uniform heating. That’s why induction heating equipment leads the way. The Miller ProHeat 35 with a Rolling Inductor System can induce the electromagnetic field into the metal, heating it from within while the vessel is rotated. It significantly reduces the risks while increasing the time to temperature and helps improve product quality and code compliance.
The downstream sector requires the use of all welding processes. If you manufacture large pressure vessels or storage tanks, you’ll need sub-arc welders, seam welders, and welding tractors. Or, if you weld specialised alloy process piping, you may need advanced TIG welders (e.g., Miller Dynasty 400) and closed or open-head orbital welding equipment. Your welding technology needs may vary greatly depending on the specific downstream application. Reach out, and our in-house experts will help you pick the most productive welding equipment for the alloy and the piece of equipment you are working with.
Commonly welded equipment:
- Pressure vessels
- Hydrocracking and desulphurisation reactors
- Pipes, tubes, and elbows
- Valves
- Storage tanks
- Heat exchangers
- Structural members
- And much more!
Commonly welded materials and alloys:
- Carbon steels
- Stainless steels (lean, standard, super, duplex, martensitic, super-austenitic)
- Cobalt alloys
- Titanium alloys
- Specialised steels
- High strength, creep resistant, and cold tough steels
- Aluminium
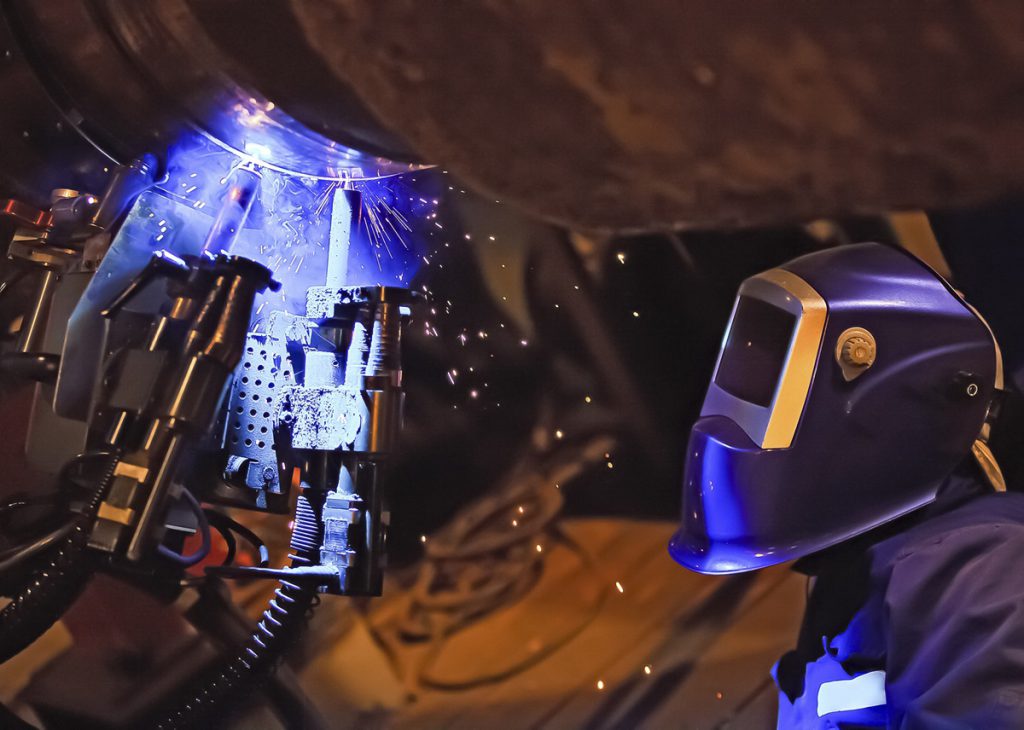
The Most Beneficial Automation Equipment For Oil And Gas Welding
Welding automation in the oil and gas sectors is critical for efficiency and profitability. While manual welding still has its place, almost everything is automated nowadays. Weld defects can cause extreme capital loss and significant safety risks in many oil and gas equipment. The only way to ensure quality is through accurate repetition of the welding processes, and automation does just that!
Welding Tractors
Welding tractors travel along a set rail and carry the welding torch. You can use tractors for long seam welds in storage tanks or circumferential welds on pipes and vessels. One of the most popular welding carriage systems is the Gullco GK200. It’s ideally suited for storage tank and pressure vessel welding with an oscillating gun motion.
Pipe And Pressure Vessel Rotators
Pipe and pressure vessel rotators allow you to safely rotate heavy round objects with uniform rotational speed. You can pair rotators with a welding manipulator to create an automated welding system for maximum weld accuracy and uniformity.
Orbital Welders
Orbital welders are irreplaceable for welding small and large-diameter pipes and tubing. They are especially beneficial when welding a large number of pipes, like when fabricating heat exchangers and process piping. Orbital welders guide the TIG electrode or the MIG/Flux-cored torch as it travels around the circumference of the pipe and produces a highly uniform, clean weld. Learn more about orbital welding applications in our separate article.
Pipe Saws
Pipe saws allow you to cut and bevel pipes with maximum accuracy. Even minimal discrepancies in cut quality can cause pipe welding defects. Orbital pipe saws can make the weld preparation process much faster and eliminate rework.
Column And Boom Manipulators
Column and boom manipulators control the welding head in a standalone configuration or paired with other automation equipment like positioners and rotators. For example, the Bode TRMB column and boom with Lincoln Electric SubArc DC power source is ideal for welding large reactors, pressure vessels, boilers, storage tanks, and other massive equipment that requires heavy-duty welding.
Welding Positioners
Welding positioners allow you to position the workpiece and rotate it for an ergonomic approach and consistent weld quality. For example, you can use a positioner to weld flanges to pipe ends or smaller pressure vessels used in petrochemical processing.
Weld Cladding Stations
Weld cladding stations are irreplaceable for pipe, vessel, heat exchanger, and storage tank cost reduction. You don’t always want or need to use costly alloys for the base metal of such equipment. So, you can use carbon steel and line it with a corrosion-resistant alloy to make it corrosion-resistant at a fraction of the cost.
Cladding equipment can have a small-footprint too. For example, the Fronius FPA 9000 Compact Hot Wire Weld Cladding Station or the Cladding Station With an HMI-T10CC Controller can fit in a smaller shop or work on-site when possible. It’s perfect for cladding pipes, heat exchangers, and tanks.
Westermans International: Your Reliable Partner For Welding And Cutting Equipment
No matter where you are in the oil and gas industry, Westermans International can help you obtain the most suitable welding equipment. You need adequate tools to maximize your productivity and bottom line. Contact us today, and our team will help you choose the equipment for your next pipe, pressure vessel, tank, heat exchanger, or other project you are working with.
comments
I am a welding
I can weld very well
Am from Nigeria
I am interested
Hello,
We do not undertaking welding operations here, we sell welding and fabrication machines. Good luck with your search.
Thanks For the best post very useful information .Thank you for sharing this post and help full content.
Thank you for your kind comments 🙂