With many different types of weld joints and terms, how do you know which is the right one for your job? This basic guide should help to develop your knowledge further.
Please note that this introductory information. Those who intend on welding professionally, we advise to study the required process in more detail. Click here to visit TWI website for further study.
Careers in welding and fabrication involve many sectors; from structural steel construction to exhaust manufacturing for the automative industry. All metal fabrication industries use a variation of these welding processes.
How do you know which type of weld is right for your job?
There are many different joins and terms used to describe individual welding types. It’s important to gain some basic knowledge and understanding of these, as they all have specific uses.
Not all welds can be used on all joints.
Hopefully the following will shed more light, specifically for beginners learning the ropes! Get your welding projects off on the right track with our simple guide…
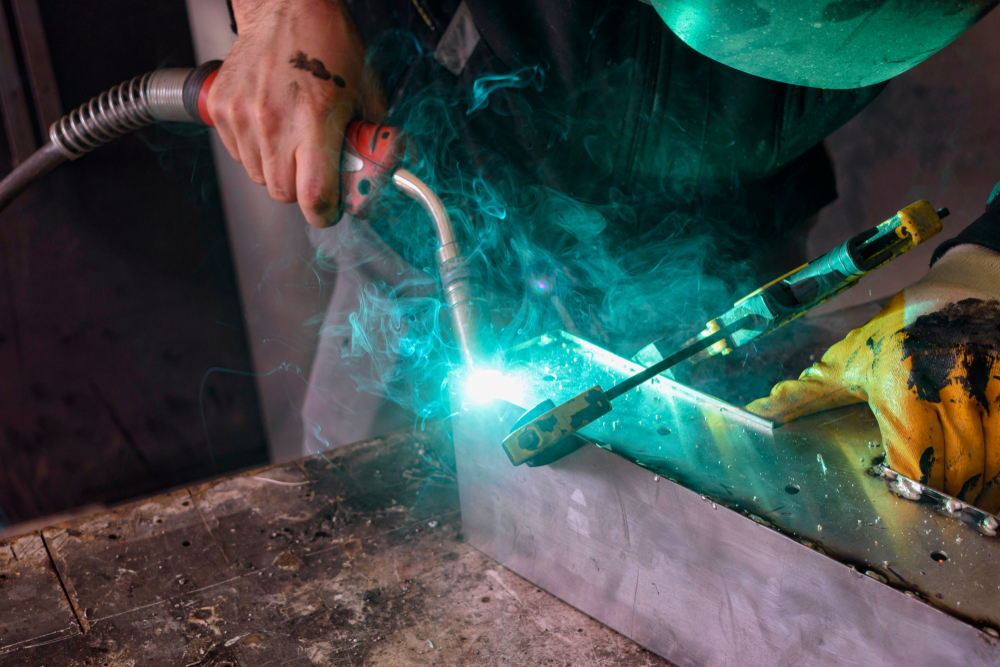
Fillet weld.
Best For: All common welding tasks except butt joints.
The most common type of weld and easiest to learn is the fillet weld.
Related to the MIG welding process, it can be used for a wide variety of joints. It’s suitable for an array of DIY projects or professional applications, due to its strength and versatility.
So whether you’re ending at an angle, overlapping two metal sheets, or joining the end of a cylinder.
It’s also an advantageous weld when speed is required, as little weld preparation is need and strong welds are achieved quickly.
Click here for our range of used and refurbished MIG welders for sale.
Groove weld.
Best for: welds where strength is critical.
Not to be mistaken for a fillet weld, a groove weld has comparable applications, and is formed in much the same way. However, it is much stronger.
Penetration of a groove weld is much higher than a fillet weld, making it an ideal type of weld for industrial applications.
The join requires more effort in preparation, to develop the deep groove required. Creating a U or V – shaped bevel on each piece of metal with a bevelling tool will make the groove depth needed.
When joined, the groove will be filled with molten metal on welding, thus creating a thick, penetrative weld.
Groove welds are also called bevel welds.
Plug weld.
Best for: large or thick materials that won’t be subject to heavy loading.
Used to join two metal workpieces that overlap, such as welding exhaust pipes onto vehicles. It comes in handy when a spot welder has insufficient reach, or doesn’t have the required power to penetrate thick components. One of it’s most common uses is in the automotive industry, with results sometimes stronger than a spot welded alternative.
Using a drill or a plasma cutter, holes are created in the top workpiece. Using a clamp, this is then placed over the base component, and the join created by the holes being filled with weld material.
Slot weld.
Best for: when more strength is needed than a plug weld.
Comparable to a plug weld, a slot weld is basically an elongated version. When preparing the top piece, a slot is made instead of a hole. This increases the contact area for the weld material, thus increasing the strength. It can either be open ended or enclosed.
A disadvantage to a slot weld when compared with a plug weld, is it requires significantly more weld material, making it a more expensive process for bigger jobs.
Surfacing weld.
Best for: strengthening/repairing damaged surfaces.
As might be concluded from the name, a surface weld isn’t a join as such. This type of weld is used to deposit weld material onto a surface. Applications include filling holes and gaps from corrosion for example. It is also a good solution for hardening and strengthening existing components through the layering of weld material.
The process involves running one (or multiple) weld beads over the base material, until the desired thickness is achieved. These can then be finished by grinding for additional processes such as plating or painting.
These five weld types are the most commonly found in general use.
The following most likely to be found in manufacturing and other production environments, and are more specialised.
Spot welding.
Best for: production welding of thin sheet, not subject to large loads and stresses. Particularly in the automotive industry.
A resistance welding process, a spot weld is formed when an electrical current passes through two points (electrodes or tips), either side of two sheets of metal. This current melts the metal, joining them together. Similar to pressing your index finger and thumb together. It’s ideal for joining thin metal sheet, usually up to around 3mm in thickness. A fast process that can combine multiple spots to “stitch” 2 workpieces together.
The welding machines come in various forms, hand-held or stand-alone machines depending on the application.
Different tooling can be added to suit the requirement, with some standard arc welding machines also featuring spot welding functions.
Click here for new and used spot welding machines for sale, or find out more about the process here.
Seam weld.
Best for: overlapping joints on components where a continuous, secure weld is required. For example liquid or gas vessels.
Similarly to spot welds, circumferential seam welds can also be formed via the resistance welding process. However, the weld is formed with a continuous line, as opposed to multiple individual welds.
For longitudinal seam welds, an arc welding power source is required to create the electrical current. Longitudinal welds can be made with MIG, TIG, SAW and PAW processes.
Seam welding is most commonly used in the manufacture of tanks and vessels that need to contain gasses or liquids (including hazardous material).
Click here for circumferential and longitudinal seam welding equipment for sale.
Flash weld.
Best for: railroad and pipeline construction.
A much more specialised type of weld, a flash weld doesn’t use any type of filler material, such as a rod or filler wire. Instead, a flash weld is produced by heating the ends of two metal workpieces using the resistance process. The addition of intense pressure causes excess metal to be ejected from the area in a series of flashes, fusing the two workpieces together. It is also known as flash butt welding.
Upset weld.
Best for: production requirements needing a high-quality weld.
Another form of a resistance butt weld, an upset weld is similar to a flash weld, but on lighter, smaller components.
Workpieces are clamped together, with an electrical current and pressure working to “upset” the metal components, fusing them together.
Upset weld characteristics include a very small weld area that is consistent in high quality, due to it being a usually automated process. Applications include joining steel tubular rings and hoops, such as gas burners and alloy wheels.
Conclusion.
Using the correct type of weld is vital for the strength and durability of the finished result. The type of weld required will much depend on the final use of the job, taking into account characteristics needed.
The type of joint to be used might also affect the type of weld for your job, we will look at this next.
It’s also important to research the best welding machine for the application.