Automotive welding in production and repair relies on multiple welding processes to meet the regulatory and manufacturer’s standards. Welding technology selection is critical for welding advanced steels, aluminium, and magnesium alloys that are widely used in modern vehicles.
Without welding, there’d be no cars or heavy transport vehicles, especially not the modern cars we all love to drive. Likewise, without advancements in welding technology and innovative ways of applying it, your car would have a reduced fuel economy and higher emissions. Automotive welding has far-reaching effects, not just those regarding the vehicle’s structural integrity.
Welding Processes In The Automotive Industry.
Car manufacturing and repair require working with several welding processes, depending on the welded component and material. All welding processes have pros and cons. However, some methods are inherently far more economical for specific tasks.
Besides passenger cars, transport vehicles like dump trucks, feed/grain trailers, flatbeds, trash trucks, liquid haulers, and other heavy transportation vehicles require welding for production, repairs, and custom jobs. Arguably, the welds holding heavy transport vehicles together are even more critical as their failure could cause significant damages and traffic accidents, especially since these vehicles travel with high loads and speeds on expressways. Likewise, the liquid tankers can hold hazardous, flammable, or explosive compounds. So, any repairs or custom jobs on a tanker must be done with high quality equipment and according to all applicable standards.
Resistance Spot Welding (RSW).
By large, resistance spot welding is the most widely used joining process in the automotive industry. As the name implies, RSW uses resistance to the flow of the current to melt metals. You can use various electrode shapes to deliver the current and apply pressure to fuse the two materials in a spot. The weld is in the form of a nugget where two sheet metals coalesce into a spot joint.
Unlike arc welding, resistance welding happens in less than a second. This is critical for working with high-strength steel (HSS) and ultra-high-strength steel (UHSS). Many car manufacturers mandate or recommend using a spot welder for collision repairs because its quick and low heat input is less likely to cause weld hardness and the loss of mechanical properties.
Spot welding machines come in many sizes and setups. You can use a suspended spot welder to freely move it around the vehicle or a fixed, free-standing spot welder which requires bringing a part to it. Spot welders can also be portable, making it easier to do auto body repair jobs.
You can apply spot welding for various car, van, and truck body assemblies in repairs and custom jobs. Auto services can benefit from small spot welders specifically designed for manual work on vehicles. For example, the PEI Carpoint 11 RF PX1700 is mounted on a trolley and supports single-sided and standard spot welding. When paired with a car body pulling kit with a sliding hammer, you can even pull out dents using the single-sided spot welding gun.
There are tens of ways spot welding is used for car bodywork. It can be the most critical piece of equipment an auto shop can have.
Besides bodywork, resistance welding is used for elements like heat insulation for exhausts, especially for sport vehicles. Insulating the exhaust system helps keep the heat inside, protecting other engine components and increasing the expulsion rate of exhaust gases. Sport vehicle engines can be complex and challenging to install insulation. This is where the low profile of the FastSpotter Single Sided Resistance Welder can help significantly. Not only is it easy to access the difficult geometries, the roller seam wheel attachment creates the perfect solution for joining the insulating mesh and heat shields.
Stud Welding (SW).
Stud welding is another resistance welding process, but it’s applied for fusing studs to the surface of the material. The resistance to the flow of electricity melts the base metal and the stud’s surface at the point of contact, while the stud gun plunges the stud into the weld area.
Car parts like the wiring and heat source insulation, heat shields, power steering system, exhaust, and airbags require stud welding. Likewise, you can only reliably weld broken studs with a stud welder during repairs.
Gas Metal Arc Welding (GMAW/MIG).
MIG welding is a semi-automated welding process that uses a wire and a shielding gas. Wire acts as an electrode and a filler metal, so you can’t make autogenous welds like with spot and TIG welding. The MIG shielding gas protects the weld metal from atmospheric oxidation.
Cars are commonly welded with robotic MIG welding during production. Auto repair services also often rely on manual MIG welding for car panel and structural repairs. MIG welding is also critical for heavy-duty trailers and semi-truck repairs. Frame, trailer, exhaust, and suspension repairs for trucks is critical for longevity of the heavy transport vehicles.
The biggest benefit of MIG is its high welding speed. Standard MIG can introduce too much heat for certain metals and thicknesses used in the automotive industry. However, using advanced pulsed MIG welding can help reduce the heat input. Feature-rich MIG welders from brands like Migatronic, GYS, Fronius, Lincoln Electric, Kemppi, ESAB, and Miller, can have highly accurate pulsed modes (depending on the model).
Gas Tungsten Arc Welding (GTAW/TIG).
TIG welding is an extremely precise welding method often used where weld aesthetics matter. It uses a non-consumable tungsten electrode and a shielding gas, and can be applied with or without a filler wire.
While TIG concentrates high heat into the weld joint, the operator can control the energy input in real-time using the TIG foot pedal. Likewise, the welder can manually dab the filler wire into the weld pool and have a high influence over the weld shape and size. The tungsten electrode never touches the material, which is the primary reason you can achieve high weld quality with TIG. Auto shops usually use TIG for stainless steel custom exhaust pipes and components that require high weld accuracy, like suspension parts. TIG is also indispensable for precision repairs of critical truck and heavy vehicle components.
Like MIG, TIG can be pulsed with advanced TIG welders. Both MIG and TIG are excellent choices for aluminium components. However, TIG has the advantage of higher accuracy and aesthetics. You’ll need an AC TIG to weld aluminium, while DC TIG works for steel and stainless steel.
Laser Beam Welding (LBW).
Car manufacturers use laser welding for parts like AC equipment, transmission, engine components, fuel injectors, and body parts. The automotive industry mainly uses CO2 and Nd:YAG laser types with exceptionally powerful equipment (up to 60KW). Likewise, laser cutting is critical for high-precision vehicle part manufacturing.
High-capacity laser welding and cutting equipment isn’t economically viable for relatively low production or repairs. However, handheld fiber laser welders have become more accessible. You can use welders like the XTW-1500 Fiber Laser Welder to make excellent welds when making custom parts, like tubular stainless steel assemblies for frames or exhausts.
Brazing.
Brazing isn’t welding. It’s a different metal joining process that doesn’t melt the base material; it only melts the filler metal. However, brazing can be done with almost any conventional welding method like MIG, TIG, or Oxy-fuel. You need to set your welding equipment to input just enough heat to melt the filler metal, but not the parent metal.
Some car manufacturers require brazing for collision repairs to prevent the base metal from undergoing negative metallurgical changes. Since the metal never melts, it keeps its original properties.
Friction Stir Welding (FSW).
Friction stir welding is an advanced welding method used for welding alloys that are highly susceptible to metallurgical changes with heat input. FSW heats materials to their plastic state by a rotating tool and mixes them along the seam line.
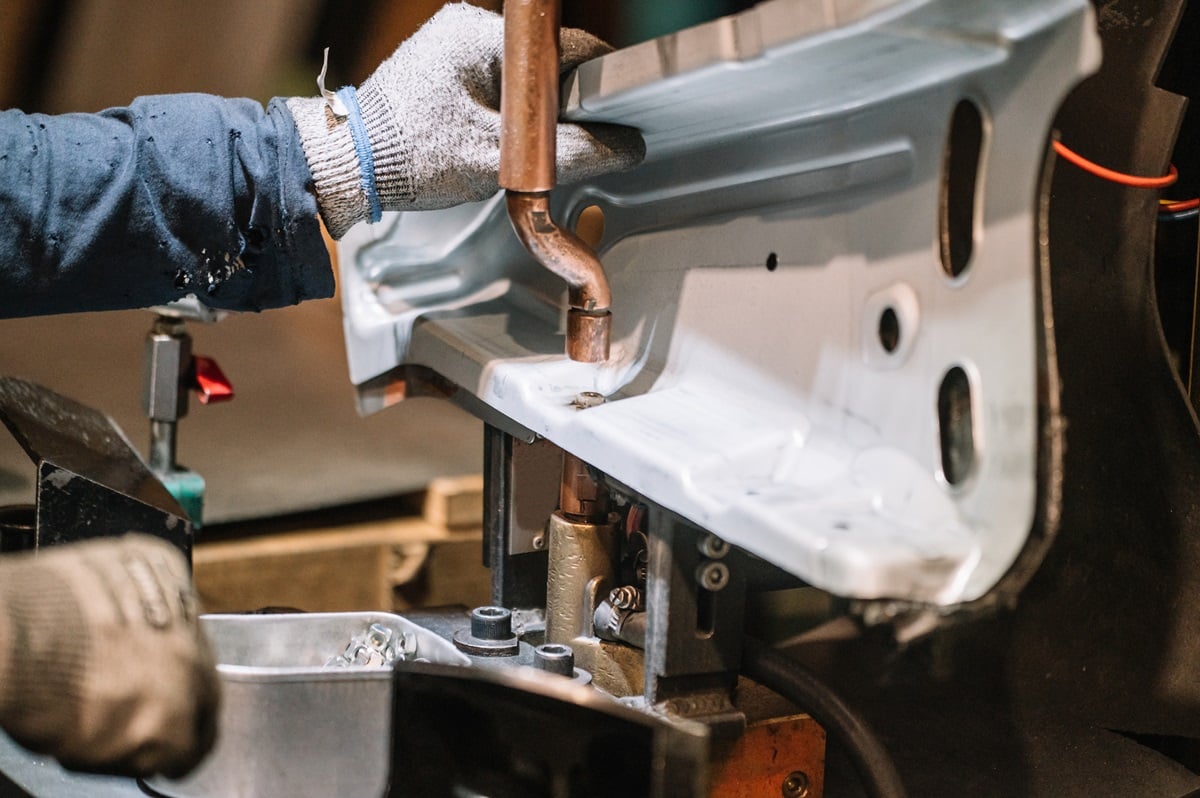
Welding Applications in Automotive Production And Repairs.
Welding processes are used in almost every vehicle part from structural frames to the exhaust system. In production almost every part of automotive welding is automated. However, if you run an auto service or produce custom or replacement parts, you’ll typically use manual welding processes.
Welding for production or repair is primarily used for these vehicle components:
- Structural frames.
- Auto body parts like fenders, hoods, roofs, and bumpers.
- Truck trailer cross members, body patches, and reinforcements.
- Trailer production and repairs.
- Exhaust system.
- Suspension.
- Radiators.
- Fuel tanks.
- Battery assemblies for electric vehicles.
- Wheels and the drive-terrain system.
Trust Westermans For High-Quality Welding Equipment.
Whether you are looking to buy or sell welding equipment for automotive welding, Westermans International is here for you. We supply a wide range of top-notch resistance welders from PEI and other brands, and MIG, TIG, and sometimes laser welding power sources.
Contact our team, and our experts will help you determine the most suitable welding power source for your application. Got some automotive welding equipment you’re looking to sell? Send us details here.