Introduction: What are Pipe Rollers and What Are Their Benefits for Welding?
Pipe rollers are an essential piece of welding equipment, used to create a secure and uniform weld on pipes. They help to ensure that the pipe is held in place while welding, resulting in a stronger and more reliable weld. Pipe rollers, also known as pipe rotators, provide other advantages for welding. Such as increased safety and accuracy, improved productivity, and reduced costs. This article will provide an overview of pipe rotators and the various benefits they offer for pipe welding.
How to Choose the Right Pipe Rollers for Your Project.
Choosing the right welding rotators is essential for a successful outcome. The type of roller you choose will depend on the specific requirements of your project.
There are various types of rollers available. So it’s important to consider all factors before selecting the best option for your needs. These include load capacity, material type, and compatibility with other components.
Conventional welding rotators are most common, a simple roller bed system that the pipe sits on. They are available in a large range of diameter capacities. As well as the option for PU or steel wheels, making them suitable for most pipe welding projects.
Another type used in industrial welding of cylindrical components, is self-aligning rotators. The wheels automatically align themselves, making them ideal for vessels that have ovality. Again, self-aligning rotators come in a range of diameter capabilities and wheel types.
The Benefits of Using Pipe Rotators in Welding Processes.
Pipe rollers are an important tool in welding processes, providing many benefits to improve weld quality.
Pipe rollers make it easier to position pipes for welding. Thus helping to ensure that the welds are even and consistent. They also allow for faster weld times, as they reduce the amount of time spent on positioning pipes. Furthermore, they help to improve weld quality, by reducing the amount of distortion caused by heat during welding.
Tips & Techniques for Effective Use of Pipe Rollers in Welding Projects.
Knowing how to use pipe rotators effectively can be crucial for a successful welding project. Some tips and techniques on how to use pipe rollers in welding projects include:
- Ensure correct positioning during the welding process
- Align the material and roller during fit-up stage
- Check the weight of the workpiece before loading onto the rollers
- For long pipes, will extra idler supports be needed to ensure proper weight distribution?
- Do the pipe rollers have the correct speed capabilities for your project? This will be dependant on the welding process you’re using.
Common Challenges & Solutions When Working with Pipe Rollers.
Pipe rollers are used in the welding process to ensure that pipes join together properly. Yet, there are some challenges that can arise when working with pipe rollers.
These include difficulty in aligning the pipes, and controlling the speed of the rotator. As well as potential damage to the welded area. Fortunately, there are solutions to these problems which can help.
Making welding rotators more efficient and effective tools for welding. Some of these solutions include using adjustable speed control systems. This makes turning the pipe smoother and more regulated. Also using guide rails to help align pipes, and using high-quality materials for the rotator itself. Understanding these challenges and implementing appropriate solutions is vital. Welders can ensure they get optimal results from their pipe rolling process. Thus improving their welding and fabrication capabilities as a whole.
Click here to see how one of our customers in the engineering sector uses their pipe rotators as part of the welding process.
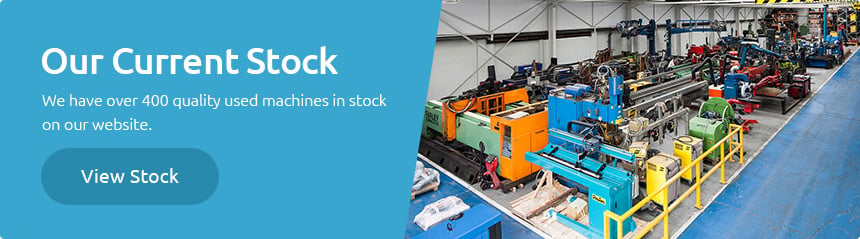